Adhesion system
model (What is stickiness?)
Many people asked me about what kind of material the sticky pads
made out of and there is a large spectrum of surface energy. As I
learned more about molecular mechanics, however, it is
getting more convincing to me that adhesion is depends
more on geometry of structures than the type of material.
In the beginning of RiSE (Robots in Scansorial Environment)
project, winter of 2003, I was wondering about the mechanism
why sticky stuff stick on surfaces. What feature makes
things sticky? My hypothesis was that the more compliant the
structure of a system, the stickier it is. One approach
drawn from this concept is very simple
Adhesion system model that I made in Jan 2004.
Hierarchical compliance system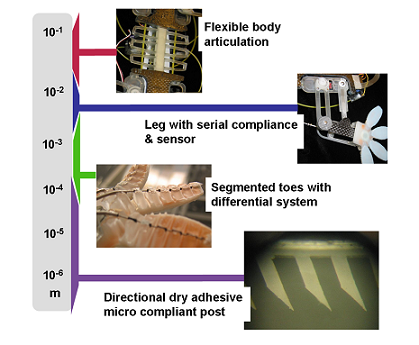
As mentioned in adhesion model, surface conformation is essential in adhesion since
Van der Waals force is
very weak unless there is intimate contact between two
surfaces. Van der Waals force is known to be very weak,
although its usage is ubiquitous in our life. Most common
example is conventional tape that uses very soft material
for compliance.
Vertical climbing on various surfaces requires more
sophisticated system than single thin layer of soft polymer
used in tape. In natural and artificial
environment, roughness in many length scale is presented.
Thus, in order to maximize the number of molecules in
intimate contact between feet and wall surfaces,
corresponding length scale compliance is needed. Gekco species
also present hierarchical compliance in their body. Flexible
body and leg can conform at the centimeter scale. Toes
and soft skin are responsible for 1~2 millimeter scale.
Within a millimeter scale, specialized hair structures are
composed of lamellae, setae and nano scale spatulae covering
up to nanometer scale. Stickybot inherits similar
characteristic comprising 12 active actuator, 8 DOF serial
and 4 passive compliant DOFs in leg and 16 segmented toes
controlled via two stage differential cable driven system.
Directional
adhesion
The most
extraordinary feature of Stickybot is Directional adhesive.
Climbing robot are not
It has Anisotropic
structure featured controllable adhesion with
directionality in adhesion force. The
movie clip demonstrates directional adhesion
compared to conventional double sided tape. Unlike
conventional tape, it sticks on smooth surface with very
small preload and is also able to detach with by
reducing load. If it is loaded in desired
direction, it creates maximum contact minimizing stress
concentration along the contact area. if it is loaded in
wrong direction, the adhesion force is very low.
Underactuated system
An
underactuated system is a system that has more number
of degree of freedom than number of actuators. Additional
degree of freedom usually controlled by either spring damper
system or differential system. Although underactuated system
is introduced in order to reduce number of actuators, in
many cases, taking advantage of passive mechanical dynamics.
A good practical example is car suspension system.
Considering a car suspension system as a robot arm, you will
find 2 DOF
- Spring
damper system
Foot design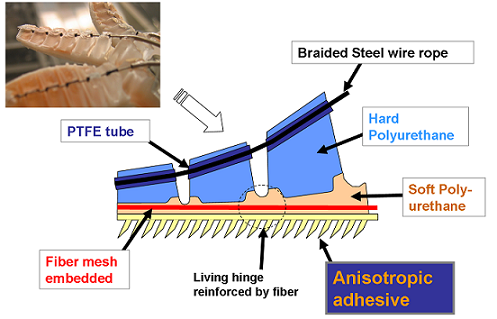
What makes
Stickybot unique is its extraordinary design of foot. Its
foot has four segmented toes controlled by single push-pull
cable via two stage differential system. Three different
polymers are used and stiffened by fine fabric to minimize
shear stress concentration along adhesive pads. It took me
about three month to finalize design iterating more than
three times. Utilizing high surface energy of poly-urethane,
we can test various adhesive pads on Stickybot feet.
Its
interesting curvature of cable path is designed carefully in
order to ac hieve well distributed normal force on the
contact area. Since each toes has seven segments, it can
conform non flat surfaces. Despite its flexible structure,
reliable adhesion requires elaborated force
transmission system from cable tension to normal pressure on
contact surface. Its desired profile is calculated in such a
way shown on the diagram on right.
Basic idea is
to create uniform normal pressure that caused by cable angle
differentiation. Each segment should have same amount of
force assuming constant cable compression force.
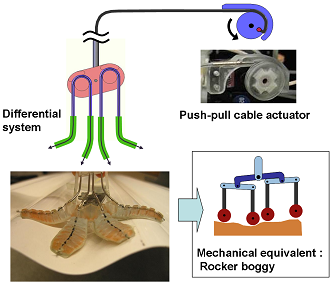
Differential cable system is employed in order of minimizing number of actuators and force balance among four
toes. One equivalent mechanical system is double rocker bogie system.Upper stage differential
actuation is rocker and one cable connecting two toes
enables lower stage differential system.
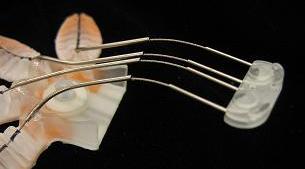
Leg design
with force sensor
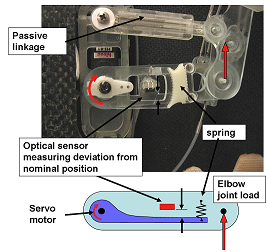
|