

กก |
What is Directional Adhesive (Gecko
Tape)?
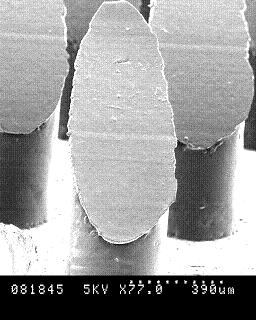
Directional
adhesion is a new innovation resulted from years of learning
from gecko's multi-hierarchical nano dry adhesive structures
as well as pondering about 'Stickiness'. It has Anisotropic
structure featured controllable adhesion with
directionality in adhesion force. The
movie
clip demonstrates directional adhesion
compared to conventional double sided tape. Unlike
conventional tape, it sticks on smooth surface with very
small preload and is also able to detach with by
reducing load. If it is loaded in desired
direction, it creates maximum contact minimizing stress
concentration along the contact area. if it is loaded in
wrong direction, the adhesion force is very low. (This
capability is also in contrast to the isotropic materials
using microfibers,
nanotubes, etc. that a number of researchers have been
developing.- Prof. Cutkosky)
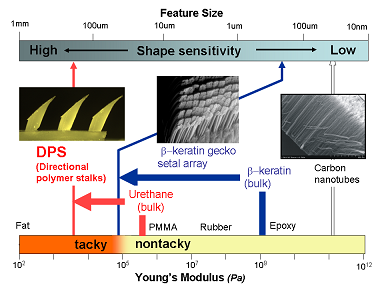
This
directional adhesive allows Stickybot to climb a range of
smooth surfaces like glass, acrylic and ceramic tile with
relatively fast speed. For a climbing robot, the role of
controllable adhesive is essential primarily because
light-weight of robot limits the maximum torque that
actuators can produce. First version was made in Sept.
2005. I did not understand essentials of adhesion and it had
very low adhesion. Alternations between design iterations
and better understanding about adhesion leads to current
design turned out to be successful. Directional adhesive is
directly inspired by the work of
Prof. Kellar Autumn on gecko adhesion.
It can clean without any additional process and has
directionality in its adhesion. Figure I shows the range of
adhesive solutions ordered in terms of feature size and
effective modulus. A material is considered tacky when the
effective modulus is less than 100kPa (Dahlquist Criterion).
Using higher modulus material which is not tacky , the
hierarchical geometry of the gecko dry adhesive lowers the
effective stiffness enough to make the system function like
a tacky material. Same principle has been adapted on
Gecko tape (Directional polymer adhesion).
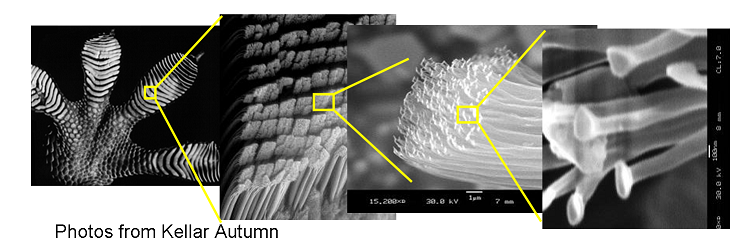
Adhesion system
model (What is stickiness?)
Many people asked me about
what kind of material do I use for sticky pads. As I
learned more about molecular mechanics, however, it is
getting more convincing to me that Adhesion is depends
more on geometry of structures than the type of material.
This is also consistent with literature. In the beginning of RiSE (Robots in Scansorial Environment)
project, winter of 2003, I was wondering about the reason
how sticky material can stick on surfaces. What feature
makes things sticky? My hypothesis was that the more
compliant the structure of a system, the stickier it is. I
came up with simple idea to test my hypothesis. Which is
very simple Adhesion system model that I made in Jan
2004.
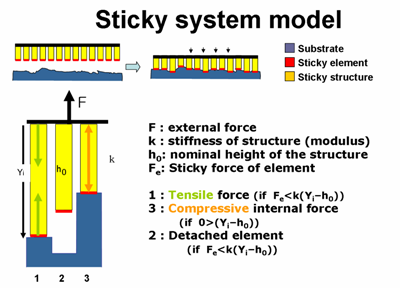 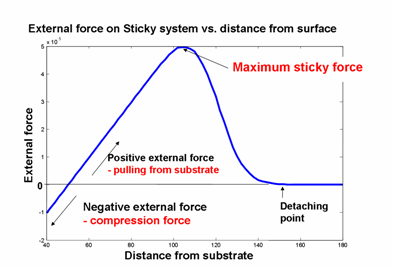
Bottom line question is
'what is
direct correlation between stiffness of the material and the
overall sticky force'. In the figure above, yellow bar
represents linear spring and red tip presents sticky
elements that remain in contact if pulling force caused by
deformation of sticky structure (yellow). After engaging
every single element on substrate, we can measure the
contact
force
increasing distance from substrate (see blue curve in graph
above). It reaches a peak when the amount of force lost my
detached elements and the amount of force gained by
stretched structures. After this peak overall adhesion force
decreases rapidly and
reaches zero when all element are detached. We can measure
maximum adhesion force at a certain condition (substrate
roughness, structure stiffness, adhesion force of element).
An interesting result yielded
from this simulation is that, with same sticky element, as
the stiffness of the structure increases, maximum adhesion
force drops drastically. This concludes that softer material
fundamentally stickier than stiffer material with same
stickiness of lower level elements. We can apply this
concept to each level of hierarchical system. I apply this
intuition on directional adhesive design.
กก
|